As you know, one of our priorities is giving drillers who use MBI products the information they need to solve issues that come up during drilling.
One of the most common problems is a plugged tube. For example, a rock might block the inside of the tube during drilling. This cuts the water off automatically.
Drillers might also encounter situations where the inner tube stops flushing. The problems are different, but the solutions are very similar.
Changes to some parts of the inner tube mounting can cause poor water circulation (blockage or flushing issues).
Here is a video from Marcelin Touzin that explains how to quickly and effectively detect problems with the water in your inner tube.
Water flow
Managing water flow in the core drill can be a challenge and cause unnecessary stops during drilling. The water needs to be able to flow properly through the inner tube to maximize the performance of not only your equipment, but your employees as well.
Once the inner tube is backed, there’s not much room for the water to flow through the assembled core barrel towards the bit.
The tube needs to be backed and adjusted properly to maximize your water flow.
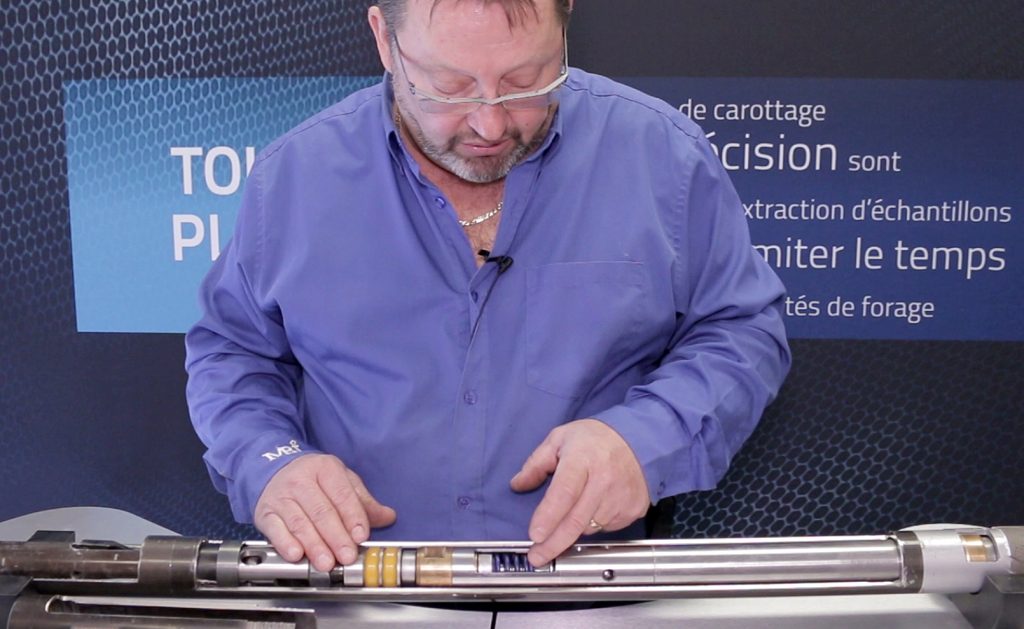
Adjusting the core lifter
The core lifter works with two shut-off valves. It needs to be adjusted properly to avoid several kinds of water flow problems.
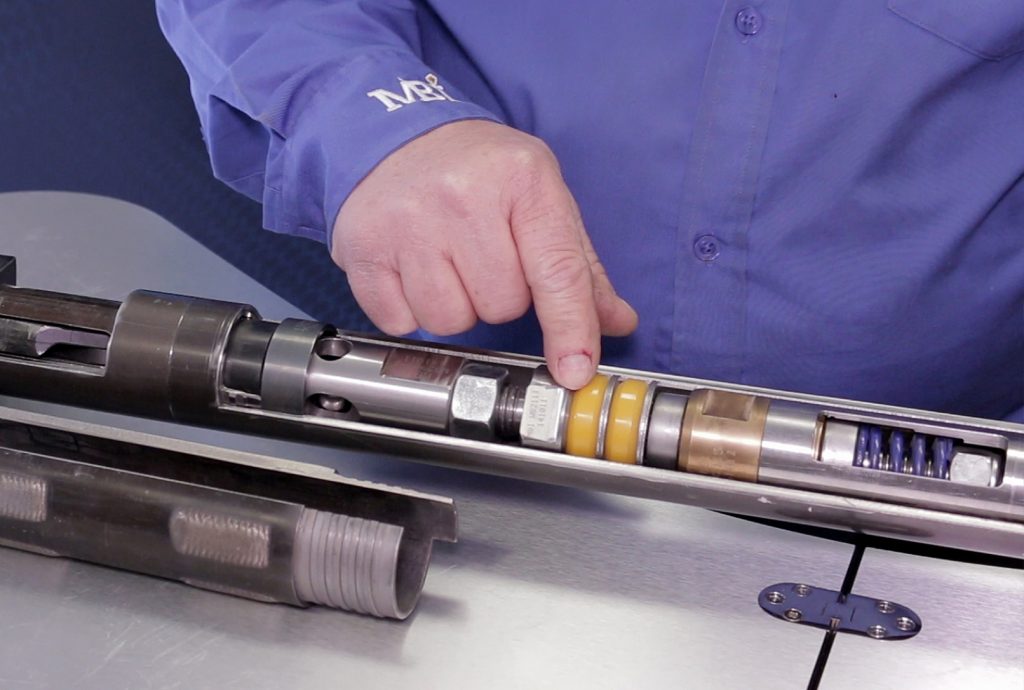
As soon as a rock blocks the tube, the tube squeezes the two valves shut and stops the water. They are a key part of the system.
As you know, it’s important to keep tightening the lifter when raising the tube to reduce unwanted space. However, if the lifter is too tight, the shut-off valves will be compromised and won’t be able to do their job properly. This, in turn, slows the flow of water in the tube.
We recommend tightening the bolt by ¾ to 1 turn.
Adjusting the backing
Leaving too much space between the tube and the drill bit is not recommended; it can even cause some water flow problems.
You need to leave ⅛–¼” (3–6 mm) between the parts to allow water to flow properly. If there is too much of a gap, the water will stop more quickly, especially in crumbly ground.
By making the right adjustments at the beginning, particularly to the lifter and backing, you can prevent water flow problems in your drill. If the information in this post didn’t help you with your water flow problems, don’t hesitate to contact us to talk with one of our representatives.