Drilling additives are extremely important allies for drillers. If drillers are knowledgeable about additives and use them properly, production will increase, the equipment used will perform better and maintenance will cause fewer shutdowns. A master driller has to stay abreast of the best techniques to optimize operations, keep equipment from rusting and prevent friction.
There are various categories of additives, and grease is an essential one for lubricating accessories and reducing friction on drill rods.
Choosing the right grease
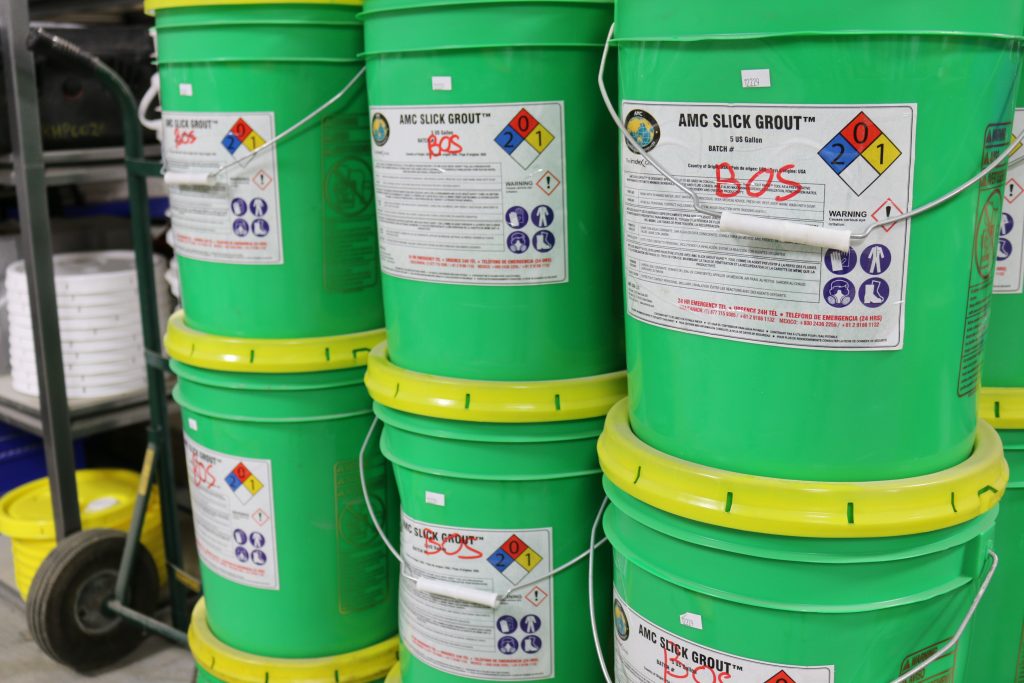
Choosing the right type of grease to use can be a headache. Depending on the geological formation in the drilling zone (types of rock, abrasiveness of the soil, pH of the water, etc.), drillers have to adapt the type and quantity of grease that they apply to the equipment. Their goal is always to optimize drilling and to ensure that the grease adheres properly to the drill rods and nets.
Today advice is available from the companies that produce additives on the right grease to choose for different rock formations. The process is simple. A technician visits the site to analyze the soil and the right grease type to apply. External help is available, along with a few training courses on mastering the art of lubrication, but nothing else can match the field experience of a master driller.
Biodegradable greases made from vegetable oil have been on the market for some time now. They are less toxic for the environment, and some mining companies prefer or even demand that they be used. Despite being made from natural ingredients, these greases offer the same anticorrosive properties and are just as effective as the others.
Mastering the right amount of grease to apply
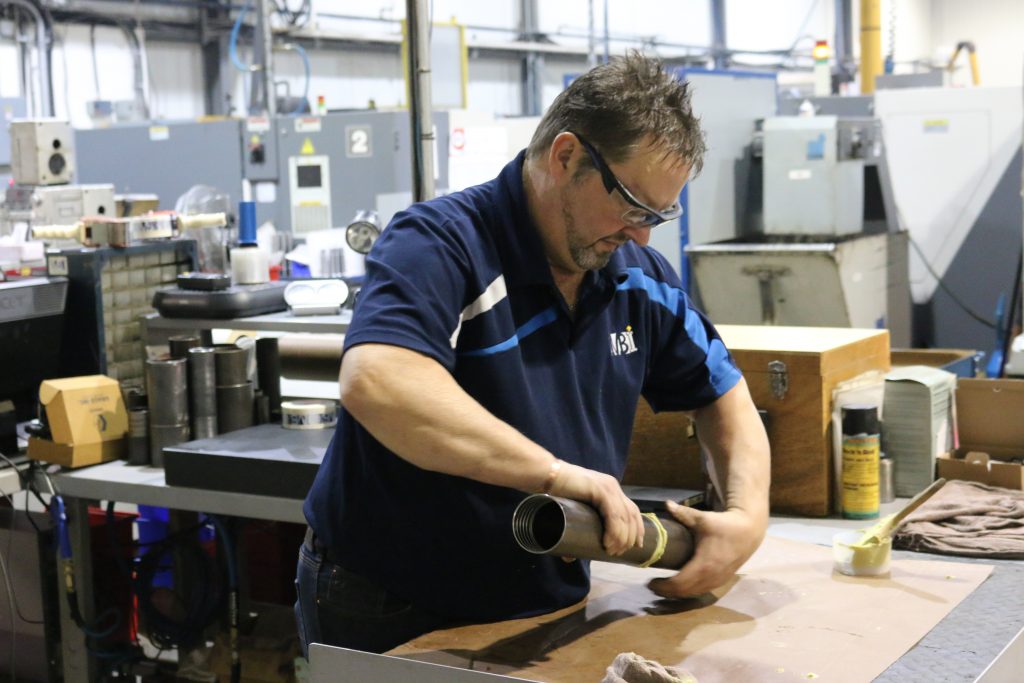
The quantity of grease applied plays a major role in lubricating drilling equipment. Ongoing improvements in the types of grease, the experience of drillers and the outside help from additive companies allow drillers to calculate the best amounts before and during the drilling.
Naturally, technicians can visit the site to identify the right amount of grease to apply. However, drillers are normally in charge of additives during operations. With their knowledge and, especially, their experience, they can determine what type of grease to use and the right amount to apply. Also, since the type of soil can vary from one metre to the next, it’s absolutely essential to adapt the grease type as drilling progresses. This takes knowledge.
The consequences of using the wrong amount of grease
Premature equipment wear, strong vibrations and broken drill rods usually result from a lack of grease. If you use the wrong amount of grease, you can actually lose a sample or reduce its quantity and quality. Sometimes the driller has to start over, slowing down production and making the project less profitable.
Would you like some advice on what type of grease to use or on maintaining your drill rods? Consult this video or contact the experts at MBI Drilling Products by email or phone.